Industries
Oil & Gas Industry
Modeling and simulation are proven ways to address the high and unsustainable costs and time required for design and regulatory approval of increasingly complex healthcare solutions. This in silico approach maximizes patient safety while making healthcare more affordable.
Accelerating Innovation in Healthcare With In Silico Medicine
The oil and gas industry is essential for global energy production, encompassing the exploration, extraction, refining, transportation, and storage of petroleum products and natural gases. To ensure safe, efficient, and sustainable operations, various analyses are required, including structural integrity evaluations, fluid dynamics simulations, impact and blast simulations, and electromagnetic field design. Ansys provides a suite of tools to address these needs, like Ansys Mechanical for structural analysis of critical infrastructure, Ansys Fluent for fluid dynamics, heat transfer, corrosion and erosion simulations, Ansys CFX for turbomachinery design of pumps and compressors, Ansys Autodyn for impact and blast simulations, Ansys HFSS for electromagnetic simulations in equipment, and Ansys Granta for optimal material selection. These solutions help engineers design, optimize, and validate systems for the efficient and safe operation of oil, gas, and alternative energy infrastructure.
- Ansys Mechanical
- Ansys Fluent
- Ansys CFX
- Ansys Autodyn
- Ansys HFSS
- Ansys Granta
Subsurface Exploration and Drilling
ANSYS delivers robust simulation solutions tailored for the demanding challenges of subsurface exploration and drilling operations. These solutions help engineers analyze complex geological formations, optimize drilling performance, and ensure safety and environmental compliance in oil, gas, geothermal, and mining applications.
Structural analysis to ensure the durability of drilling equipment under extreme subsurface conditions.
Fluid dynamics to optimize mudflow and pressure control to enhance drilling performance.
Thermal analysis to prevent overheating, extending the lifespan of drilling components.
Vibration analysis to minimize the risk of fatigue failure of components, and reduce noise levels.
Component-Level
Capabilities
ANSYS supports detailed simulation of drilling components such as drill bits, casing, mud pumps, and wellbore structures. Capabilities include geomechanical modeling, fluid flow and multiphase dynamics, thermal effects, vibration analysis, and rock-fracture prediction. This enables accurate prediction of drilling efficiency, equipment wear, well integrity, and risk mitigation in harsh subsurface environments.
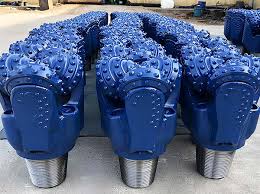
Drill Bits
- Conduct structural analysis to evaluate the mechanical performance of components, ensuring efficient and reliable drilling.
- Perform fatigue analysis to assess durability and predict failure under repeated loading conditions in harsh environments.
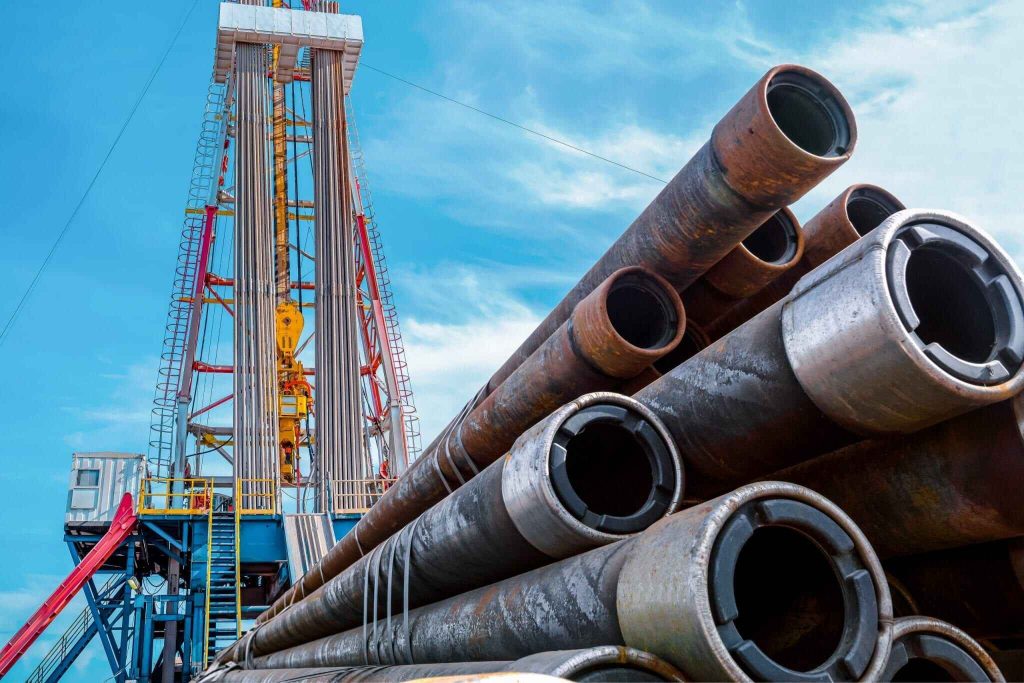
Drill Pipes
- Perform structural analysis to assess the drill pipe's ability to withstand high torsional stresses and bending forces during drilling operations.
- Simulate fluid dynamics for efficient drilling fluid circulation, ensuring proper cooling of the drill bit.
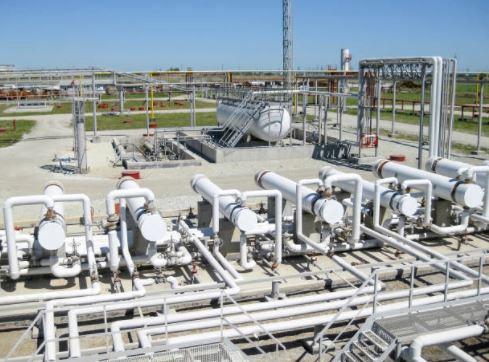
Mud Pumps
- Simulate fluid dynamics to optimize the flow of drilling fluid, improving the effectiveness of the pump.
- Perform structural analysis to assess the pump’s durability and strength under extremely high pressures and cyclic loading.
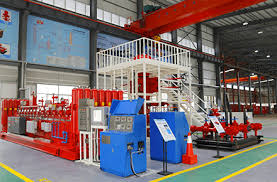
Blowout Preventers (BOP)
- Analyze structural integrity and pressure resistance to ensure BOP components can withstand extreme pressure.
- Simulate seal performance to verify sealing capability and reliability under high-pressure conditions.
Relevant Ansys
Software
ANSYS provides specialized tools such as Mechanical for structural and vibration analysis, Fluent for fluid dynamics, and Polyflow for complex flow behavior in drilling fluids. Coupled with multiphysics simulation platforms, these tools support comprehensive evaluation from drill string design to real-time drilling process optimization.
Ansys Fluent
Simulates fluid flow in drilling operations, including drilling mud behaviour, erosion, and corrosion effects on pipes and equipment, optimizing performance and longevity.
Ansys Mechanical
Performs structural, fatigue, and thermal analyses of drilling equipment and well casings, ensuring durability under high-pressure, high-temperature, and cyclic operational loads.
Ansys CFX
Simulates multiphase flows within drilling systems, such as mud pumps and separators, ensuring efficient flow assurance and minimizing cavitation risks.
Ansys LS-DYNA
Simulates dynamic events like drill impacts, accidental drops, and structural responses to extreme conditions, ensuring safety and reliability.
Ansys Discovery
Enables CAD modelling and real-time simulation for early-stage designs of drilling tools and systems, focusing on structural and fluid performance.
Ansys Twin Builder
Creates digital twins of drilling systems for real-time monitoring, predictive maintenance, and optimization of drilling operations.
Ansys Granta Selector
Assists in selecting materials for drilling equipment and pipelines, focusing on properties like corrosion resistance, fatigue strength, and thermal stability.
Ansys nCode DesignLife
Evaluates fatigue life of drilling system components under cyclic mechanical loading, ensuring long-term reliability.
Ansys OptiSLang
Automates design optimization for drilling tools and systems by integrating structural, fluid, and thermal simulations.
Pipeline Design
ANSYS provides advanced simulation solutions tailored for pipeline design and integrity management in industries such as oil & gas, water, chemicals, and energy. From structural analysis and fluid dynamics to thermal behavior and fatigue life prediction, ANSYS ensures safe, efficient, and regulation-compliant pipeline systems under diverse operational conditions and terrains.
Structural analysis to ensure the strength, reliability, and long-term durability of pipeline systems under various operational conditions.
Fluid dynamics analysis to optimize flow through pipelines, reducing energy losses and improving overall efficiency.
Thermal simulations to evaluate thermal expansion, stresses, and temperature effects on pipes and joints for enhanced safety and performance.
Corrosion and erosion simulations to predict material degradation, improve maintenance strategies, and extend pipeline lifespan.
Component-Level
Capabilities
ANSYS enables detailed simulation of pipeline components including pipes, bends, flanges, valves, supports, and insulation systems. Capabilities include flow assurance (e.g., wax/hydrate formation), pressure drop analysis, thermal expansion, corrosion assessment, vibration response, and crack propagation. This allows engineers to optimize pipeline routing, material selection, and design for long-term operational safety and efficiency.
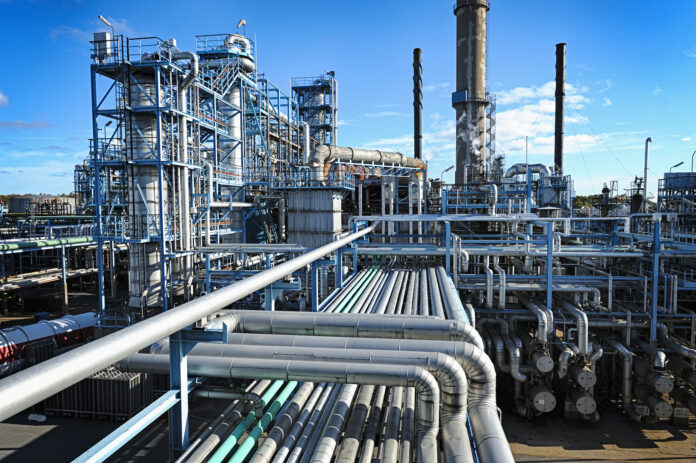
Pipe Segments
- Simulate fluid dynamics to optimize fluid flow through pipeline sections, minimizing energy losses
- Conduct structural analysis to predict and prevent leaks or ruptures caused by operational loads and external factors.
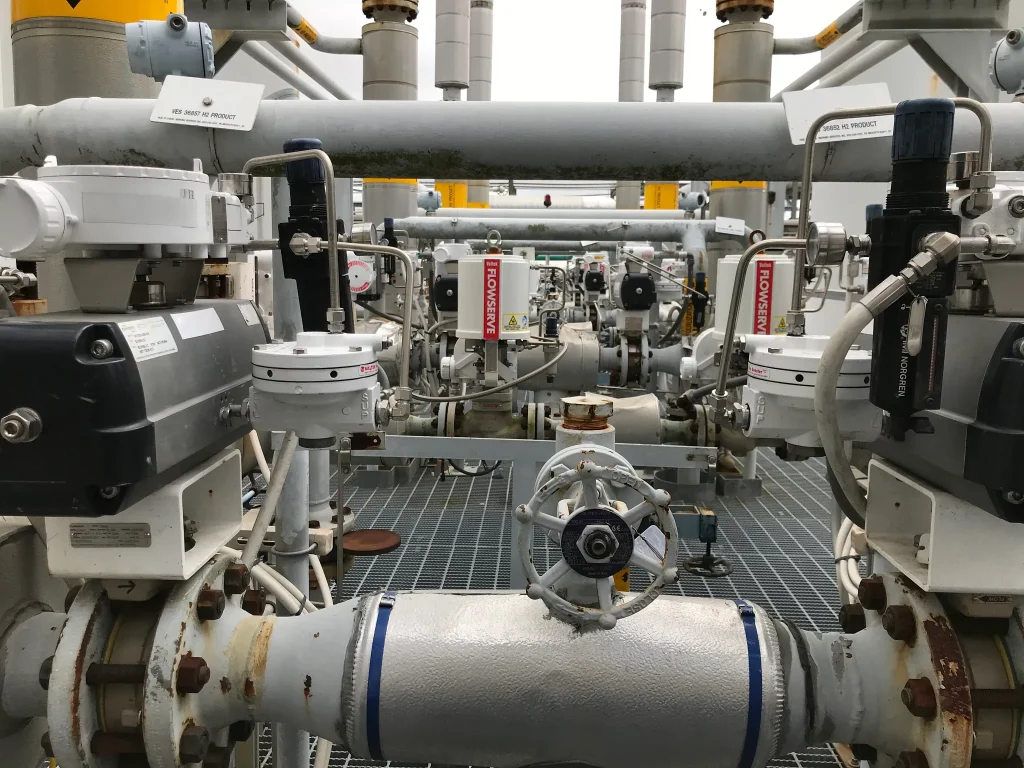
Fittings and Valves
- Perform fluid dynamics simulations to assess flow behavior through valves and fittings, and ensure precise flow control.
- Simulate corrosion and erosion to evaluate durability and resistance to wear, ensuring long-term reliability.
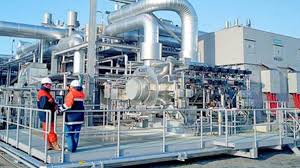
Pumps and Compressors
- Use fluid dynamics simulations to simulate flow around impeller blades, improving operational performance.
- Conduct structural analysis to verify the strength and reliability of components under varying pressure and load conditions.
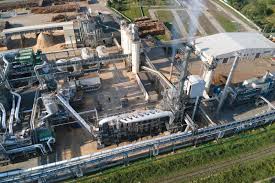
Monitoring Systems
- Analyze signal integrity and electromagnetic performance of electronics and sensors for accurate and timely detection of leaks and system anomalies.
- Simulate and validate embedded software to ensure accurate real-time monitoring, data processing, and system diagnostics.
Relevant Ansys
Software
ANSYS tools such as Fluent, Mechanical, CFX, and AQWA support multiphysics simulation of pipeline systems. Fluent and CFX handle internal fluid flow and pressure dynamics, while Mechanical simulates structural stress, vibration, and fatigue. AQWA enables offshore pipeline design by modeling wave, current, and seabed interactions—ensuring resilience in harsh marine environments.
Ansys Fluent
Simulates fluid flow, pressure distribution, and heat transfer within pipelines while accounting for erosion and corrosion effects, ensuring operational efficiency and longevity.
Ansys Mechanical
Performs structural and thermal analyses of pipelines and supports, evaluating durability under high-pressure, high-temperature, and mechanical loading conditions.
Ansys CFX
Provides advanced simulations for flow through pumps and compressors, ensuring efficient flow assurance and minimizing risks like cavitation.
Ansys LS-DYNA
Simulates dynamic events such as impact loads, pipeline bursts, or seismic activities to ensure structural safety and reliability.
Ansys Discovery
Enables CAD modelling and simulation for the early-stage design of pipelines and flow control systems, focusing on structural and fluid performance.
Ansys Granta Selector
Assists in selecting materials for pipelines based on properties such as corrosion resistance, fatigue strength, and thermal conductivity.
Ansys Composite PrepPost
Models composite materials used in lightweight and corrosion-resistant pipelines or pipeline coatings, optimizing strength and durability.
Ansys nCode DesignLife
Evaluates fatigue life and durability of pipeline components under cyclic thermal and mechanical loading, ensuring long-term reliability.
Ansys OptiSLang
Automates optimization of pipeline designs by integrating structural, fluid, and thermal simulations for enhanced performance and reliability.
Pressure Vessels and Tanks
ANSYS delivers high-fidelity simulation solutions for the design, analysis, and validation of pressure vessels and storage tanks across industries like oil & gas, chemical processing, power generation, and pharmaceuticals. By addressing critical concerns such as structural integrity, fatigue, buckling, thermal stress, and safety compliance, ANSYS ensures robust, cost-effective, and regulation-compliant designs.
Structural analysis to ensure the strength and reliability of pressure vessels and storage tanks under high-pressure conditions.
Thermal analysis to evaluate thermal expansion and stresses in the shell due to high temperatures of contained gases.
Vibration simulation to identify and minimize the risk of fatigue failure, preventing catastrophic outcomes.
Sloshing simulation to analyze the effects of liquid movement within the vessel, ensuring structural stability and safe operation.
Component-Level
Capabilities
ANSYS supports simulation of key components such as cylindrical shells, domed heads, nozzles, flanges, stiffeners, internal baffles, and support structures. Capabilities include static and dynamic stress analysis, pressure-load response, thermal and seismic analysis, fatigue life estimation, weld strength assessment, and non-linear material modeling. This allows engineers to detect potential failure zones, optimize wall thickness, and verify compliance with ASME, EN, or API standards.
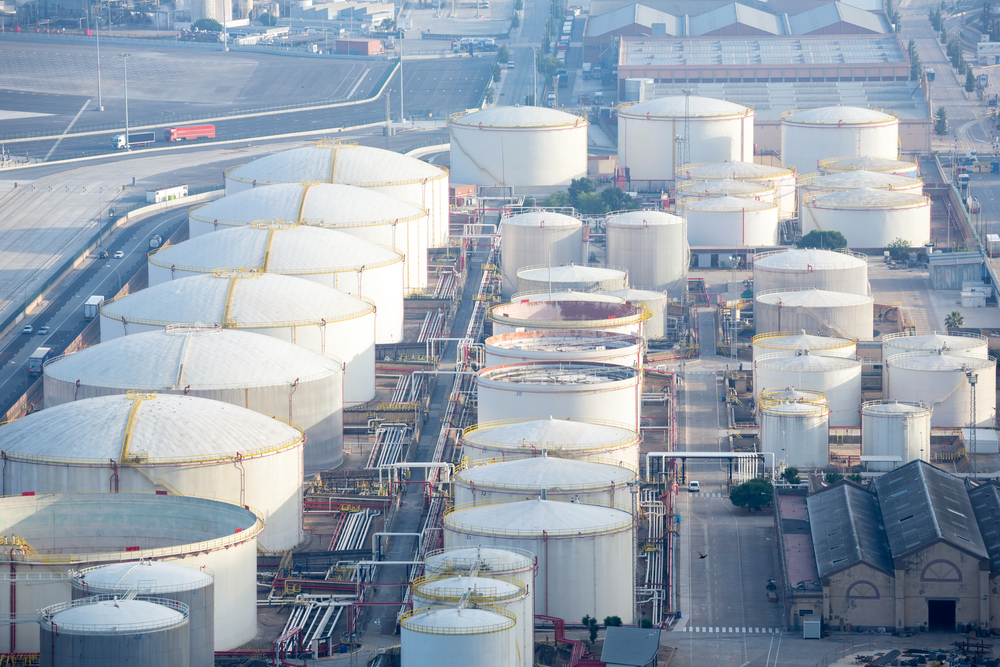
Storage Tanks
- Perform structural simulations to ensure storage tanks can withstand high internal pressures and maintain safety.
- Conduct corrosion simulations to assess the tank's resistance to long-term deterioration.
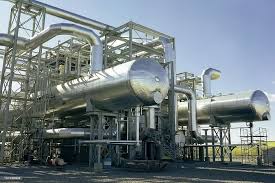
Pressure Vessels
- Assess the structural performance of vessels to ensure safe containment of gases under immense pressure.
- Perform thermal simulations to study thermal stresses, and their effect on the structural performance of the vessel and ensure safety.
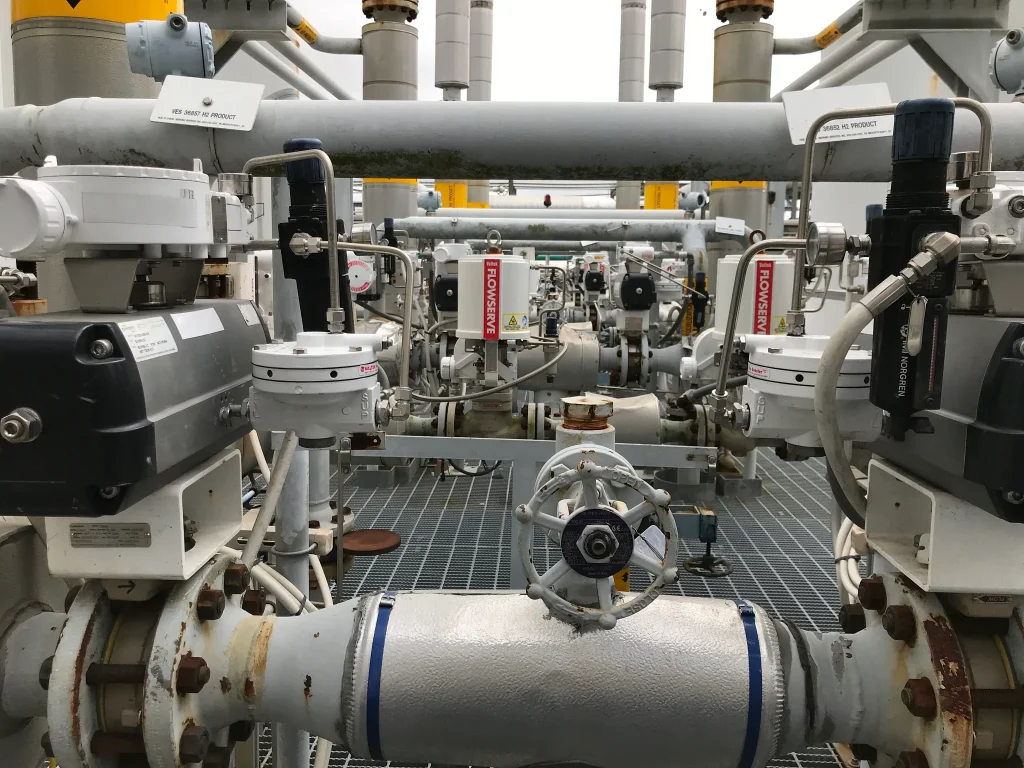
Relief Valves
- Simulate fluid dynamics to assess the functionality of relief valves in controlling excessive pressure and preventing equipment failure.
- Perform stress analysis to ensure relief valves withstand long-term operational stresses and maintain reliable performance.
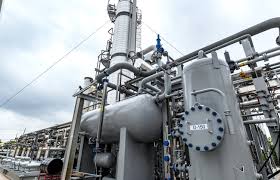
Mounts of Pressure Vessels
- Perform structural simulations to analyze the stresses in pressure vessel mounts under varying operational conditions.
- Conduct vibration and fatigue analysis to assess the durability and long-term performance of mounting systems.
Relevant Ansys
Software
ANSYS Mechanical is the primary tool used for structural and thermal analysis of pressure vessels and tanks. Additional tools like Workbench, SpaceClaim, and DesignXplorer support geometry cleanup, parametric studies, and optimization workflows. Fluent or CFX can be integrated for internal fluid-structure interaction (FSI) simulations where pressure loading varies over time or location.
Ansys Mechanical
Performs structural and thermal analyses of pressure vessels and tanks, ensuring durability under high-pressure, high-temperature, and cyclic loading conditions.
Ansys Fluent
Simulates internal fluid dynamics, heat transfer, and the effects of erosion and corrosion on pressure vessel walls, optimizing safety and longevity.
Ansys LS-DYNA
Analyzes the structural response of pressure vessels and tanks to dynamic events such as impacts, explosions, or pressure surges, ensuring safety and integrity.
Ansys Discovery
Offers CAD modelling and early-stage simulation for rapid prototyping of pressure vessels and tanks, focusing on structural, thermal, and fluid dynamics performance.
Ansys Granta Selector
Assists in selecting materials for pressure vessels and tanks, focusing on properties like corrosion resistance, fatigue strength, and thermal stability.
Ansys Composite PrepPost
Models composite materials used in lightweight, corrosion-resistant pressure vessels and tanks, optimizing for strength and durability.
Ansys nCode DesignLife
Evaluates the fatigue life and durability of pressure vessel components under cyclic mechanical and thermal loading, ensuring long-term reliability.
Ansys OptiSLang
Automates the optimization of pressure vessel designs by integrating structural, thermal, and fluid dynamics simulations for enhanced safety and efficiency.
LNG Facilities and Cryogenic Systems
ANSYS provides state-of-the-art simulation solutions for the design, analysis, and optimization of LNG (Liquefied Natural Gas) facilities and cryogenic systems. These tools help engineers address the unique thermal, structural, and fluid dynamics challenges posed by extremely low-temperature operations, ensuring safe, efficient, and reliable performance across storage, transportation, and regasification processes.
Thermal simulations to optimize insulation and minimize heat ingress in cryogenic storage and transport systems.
Fluid dynamics to ensure efficient liquefaction, regasification, and transport processes.
Structural analysis to assess the safety and durability of LNG storage tanks and pipelines under cryogenic conditions.
Vibration analysis to prevent fatigue failure in pipelines and equipment operating under cryogenic temperatures.
Sloshing simulations to evaluate the impact of liquid motion within storage tanks during transport, ensuring structural stability.
Component-Level
Capabilities
ANSYS supports detailed simulation of LNG components including cryogenic tanks, heat exchangers, piping systems, pumps, vaporizers, insulation materials, and structural supports. Capabilities include thermal contraction analysis, two-phase flow modeling, boil-off gas (BOG) prediction, fracture mechanics at cryogenic temperatures, and structural integrity under extreme thermal gradients. These simulations help reduce energy losses, improve safety, and extend asset life.

Cryogenic Storage Tanks
- Perform structural analysis to ensure tank stability under significant thermal stresses caused by cryogenic temperatures.
- Simulate sloshing to evaluate internal liquid dynamics and their effect on tank safety during transport.
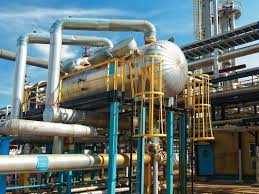
Liquefaction Units
- Simulate thermal analysis to optimize cooling processes and ensure energy-efficient operation.
- Analyze fluid dynamics to ensure the efficient flow of natural gas and refrigerants through the system.
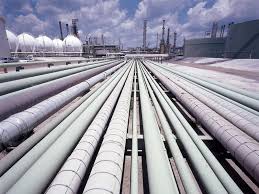
Transport Pipelines
- Simulate fluid dynamics to optimize gas and liquid flow, reducing energy losses during transport.
- Conduct thermal analysis to evaluate insulation performance, ensuring minimal heat ingress over long distances.
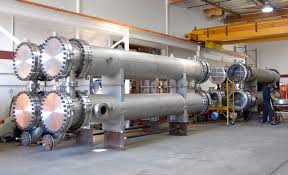
Heat Exchangers
- Perform thermal simulations to optimize the heat transfer efficiency for liquefaction and regasification processes.
- Conduct corrosion and erosion simulations to enhance the operational life of tubes and other components of heat exchangers.
Relevant Ansys
Software
ANSYS tools such as Fluent (for cryogenic fluid flow), Mechanical (for structural and thermal analysis), Icepak (for thermal management), and DesignModeler/SpaceClaim (for geometry preparation) are extensively used in LNG system design. These tools enable coupled fluid-thermal-structural simulations that reflect real-world LNG operating conditions, including rapid cooldown and heat transfer across insulation layers.
Ansys Fluent
Simulates fluid dynamics and heat transfer within LNG pipelines, storage tanks, and cryogenic systems, including boil-off gas (BOG) management, ensuring efficiency and operational safety.
Ansys Mechanical:
Ansys LS-DYNA
Ansys Discovery
Enables CAD modelling and simulation for early-stage design of cryogenic components and LNG storage facilities, focusing on structural and thermal performance.
Ansys Composite PrepPost
Models composite materials used in cryogenic pipelines or LNG systems for lightweight, durable, and corrosion-resistant components.
Ansys nCode DesignLife
Evaluates fatigue life and durability of LNG system components under cyclic thermal and mechanical loading, ensuring long-term reliability.
Ansys Additive Suite
Simulates additive manufacturing processes for creating customized cryogenic system components, such as specialized nozzles and lightweight support structures.
Ansys Chemkin-Pro
Models combustion processes in LNG flaring systems, optimizing energy efficiency and reducing emissions in LNG facilities.
Refineries
ANSYS provides comprehensive simulation solutions tailored for the design, optimization, and operational safety of oil refineries. By enabling detailed analysis of fluid dynamics, heat transfer, structural integrity, and equipment interactions, ANSYS helps refineries improve throughput, reduce emissions, and maintain regulatory compliance across critical processes such as distillation, cracking, and chemical treatment.
Fluid dynamics simulations to optimize refining processes, improve flow efficiency, and reduce energy consumption across equipment and pipelines.
Structural simulations to ensure refinery equipment, such as vessels and piping, can withstand operational stresses.
Thermal analysis to assess thermal stresses and optimize heat transfer across systems, minimizing energy losses and enhancing process efficiency.
Corrosion and erosion simulations to evaluate the influence of working fluids on refinery equipment, ensuring longevity.
Component-Level
Capabilities
ANSYS supports simulation of key refinery equipment including distillation columns, heat exchangers, reactors, furnaces, compressors, pumps, storage tanks, and piping networks. Capabilities include multi-phase flow modeling, thermal stress analysis, fouling prediction, vibration and fatigue analysis, corrosion assessment, and dynamic pressure fluctuations. These simulations help optimize process efficiency, minimize downtime, and extend equipment lifespan.
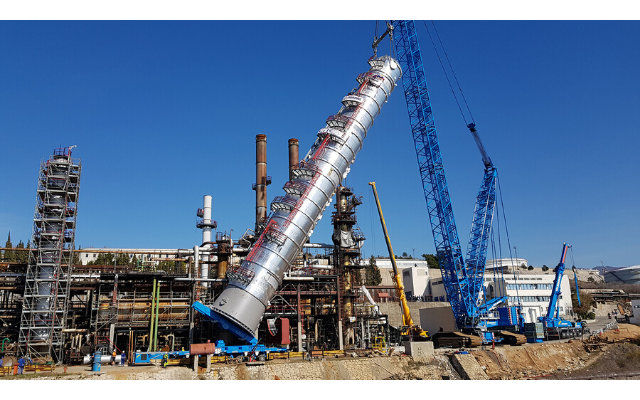
Distillation Columns
- Simulate fluid dynamics to optimize distillation efficiency, including phase transitions and flow behaviour.
- Perform structural analysis to assess the ability of distillation column components to handle thermal and mechanical stresses.
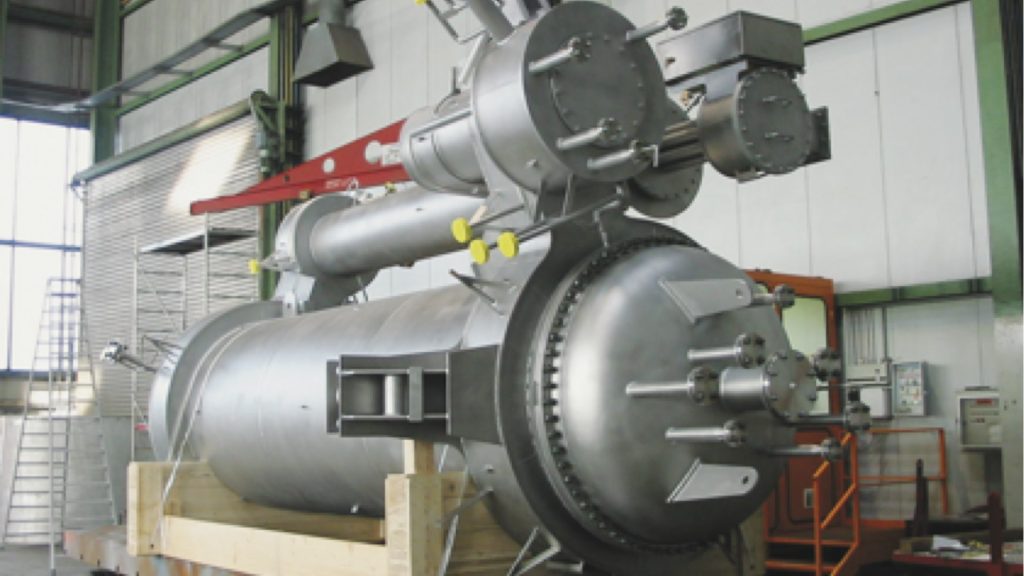
Reactors
- Simulate combustion reactions and optimize parameters for efficient burning of fuel.
- Perform thermal analysis to evaluate thermal expansion and stresses developed due to exothermic reactions in reactors.
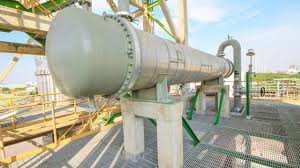
Heat Exchangers
- Perform thermal simulations to optimize fluid flow and improve heat exchange efficiency.
- Conduct thermo-structural analysis to evaluate the durability of heat exchanger components under continuous thermal cycling and mechanical stress.
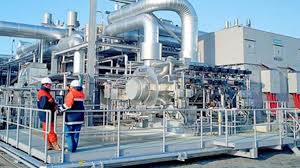
Pumps and Compressors
- Simulate fluid dynamics to ensure proper flow of fluid around the blades of the impeller, thereby improving efficiency.
- Perform structural and vibrational analysis to assess pump and compressor housing for long-term reliability and resistance to fatigue.
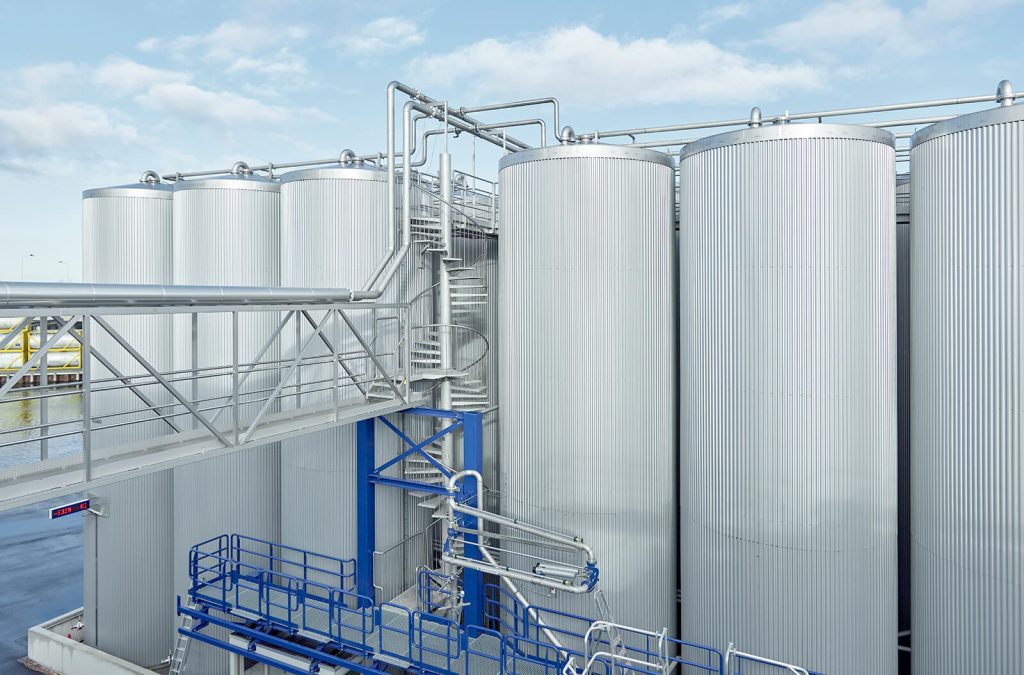
Storage Tanks
- Perform structural analysis to ensure storage tanks can withstand high internal pressures and external factors like seismic loads.
- Conduct thermal simulation to assess thermal expansion and stresses, and performance of heat insulation materials.
Relevant Ansys
Software
ANSYS Fluent and CFX are widely used for computational fluid dynamics (CFD) to model complex flow and heat transfer in process equipment. ANSYS Mechanical supports structural and fatigue analysis of vessels and piping. Tools like Chemkin-Pro enable chemical kinetics modeling for combustion and catalytic reactions, while Workbench provides an integrated environment for multiphysics simulations across refinery systems.
Ansys Fluent
Simulates fluid flow and heat transfer within refinery equipment, accounting for corrosion and erosion effects to optimize performance and extend equipment lifespan.
Ansys Mechanical
Performs structural and thermal analyses of refinery components such as heat exchangers, pressure vessels, and pipelines, ensuring durability under high-pressure and high-temperature conditions.
Ansys Chemkin-Pro
Models combustion reactions in refinery processes, optimizing operational efficiency and emissions control.
Ansys CFX
Simulates fluid flow in refining systems such as compressors and pumps, ensuring efficient process performance and minimizing flow-related issues.
Ansys LS-DYNA
Analyzes structural responses to dynamic events such as explosions, impacts, or equipment failures, ensuring safety and reliability of refinery operations.
Ansys Discovery
Offers CAD modelling and simulation for early-stage design of refinery equipment, focusing on structural, thermal, and fluid performance.
Ansys Granta Selector
Assists in selecting materials for refinery equipment, focusing on properties such as corrosion resistance, thermal stability, and mechanical strength.
Ansys Composite PrepPost
Models composite materials for lightweight and corrosion-resistant components used in refinery systems.
Ansys nCode DesignLife
Evaluates fatigue life and durability of refinery equipment under cyclic thermal and mechanical loading, ensuring long-term reliability.
interested in our Product or Solution
Still have a Question?
Qantur
FAQ
How can ANSYS improve the performance of my automotive designs?
ANSYS allows for detailed simulation and analysis, enabling optimization of factors like aerodynamics, structural integrity, and thermal management. This leads to better performing and more efficient vehicles.
Can ANSYS help reduce the time and cost of automotive development?
Yes, by providing accurate virtual testing, ANSYS reduces the need for physical prototypes and testing cycles. This leads to faster development times and significant cost savings.
What types of automotive simulations can ANSYS perform?
ANSYS can handle a wide range of simulations, including crash analysis, fluid dynamics for aerodynamics, thermal analysis for engine cooling, and NVH analysis for noise reduction.
Is ANSYS compatible with my existing CAD software?
ANSYS is designed to integrate with most standard CAD software, ensuring a smooth workflow. We support common file formats for easy data transfer and interoperability
Transform Ideas into Reality—Explore Our Simulation Solutions Today!
Partner with Us to Revolutionize Engineering Excellence!
Testimonials